Customers greatly benefit from enrolling in our post-sales services, like startup and commissioning. This ensures safe and efficient system setup. Additionally, operators and engineers can quickly grasp how to maximize system utilization. Here’s a brief overview of our services:
On-site Inspection
- Verify receiving records, packaging list, and company representative contact information.
- Inspect the equipment post-delivery, ensuring it’s free of damage and correctly labeled. This includes ensuring the appropriate labels are applied to the workstation, the user’s manual is included, and electrical connection schematics are the latest version.
- Check and verify product serial numbers. This includes the laser system serial number and the workstation serial number.
Facility Verification
- Ensure the equipment operation location is free of debris, or obstructions, and is not at risk of water incursion.
- Verify the primary and secondary coolant types (tap, tap/gycol, DI, distilled), filter size, hose size, and, or, the gas connections as applicable.
- Measure the input Line Voltage to ensure it is to the system’s specification.
- Highlight ambient dew point concerns in non-conditioned environments.
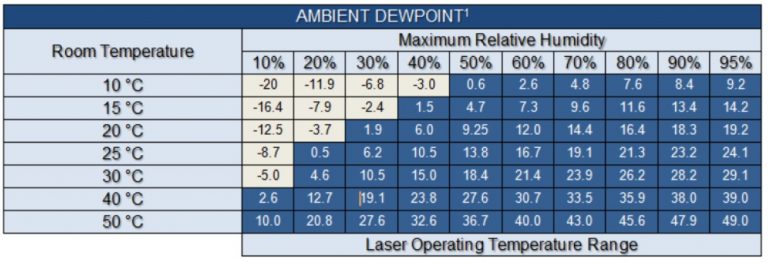
- Check for harsh environmental conditions, including extreme temperatures, excessive humidity, excessive oil and, or dust, sprinkler spray/wash, ground vibrations, electromagnetic fields, and any other conditions deemed unfit as per the equipment specifications.
- Notify the customer of any environmental conditions that may invalidate their warranty (see paragraph two of the CLC limited warranty policy).
Safety Resources
- Verify and, if needed revise, the safety protocols and management policies related to the laser system.
- Advise customer of applicable risks regarding the system, and the laser equipment’s classification level. As well as the requirements to maintain that classification.
- Verify that all safety warning labels are affixed in the correct locations.
- Advise customer on any other additional safety matters related to their laser system, including electrical, mechanical, and noise hazards.
On-site Equipment Performance Test
- Beam delivery calibration tests, including cutting or welding head nozzle coaxial centering, flat-field lens error correction, focal point verification post flat-field lens, beam collimation testing, and vision system position calibration and testing.
- Verify ancillary device operation and performance, including ensuring adequate air displacement by the fume extractor, or dust collector, the pressure and flow of assist gasses, and the airflow and humidity content of refrigerated air dryer if applicable.
- Run system performance tests, either per the standard CLC QC test criteria or per any pre-sale sample test criteria.
Training
All training courses are offered to be carried out prior to shipping at CLC’s facility in Orlando, FL. In addition, customers may opt to purchase on-site training courses.
Unless specifically stated, the customer is solely responsible for ensuring that all pre-commissioning preparations are taken care of prior to the laser system being installed. These preparations include, but are not limited to, ensuring that the chosen site can handle both a system’s size and weight, that any authorizations needed for a CLC representative to access the site have been acquired, and making any and all appropriate arrangements with local unions, including any that may exist after purchase.
However, as a solutions provider, CLC can offer our customers a tailor-made package alongside our local vendors. Typical requests include heavy lifting using cranes, plant renovations, installation of larger shutter doors, equipment anchoring for precision, and construction of gas tank stations, among others.
Please contact us with any installation requirements you may have and we will assign a project manager to you.
Service Request
Please call our service department at (866) 612-8619 to schedule a technician to travel to your facility.
If you do not wish to purchase on-site startup and commissioning you may install the machine yourself, but must take all responsibility for any damage that occurs during the installation, or due to the improper setup or operation of the system.
The customer is responsible for all technician travel expenses related to the on-site startup and commissioning.